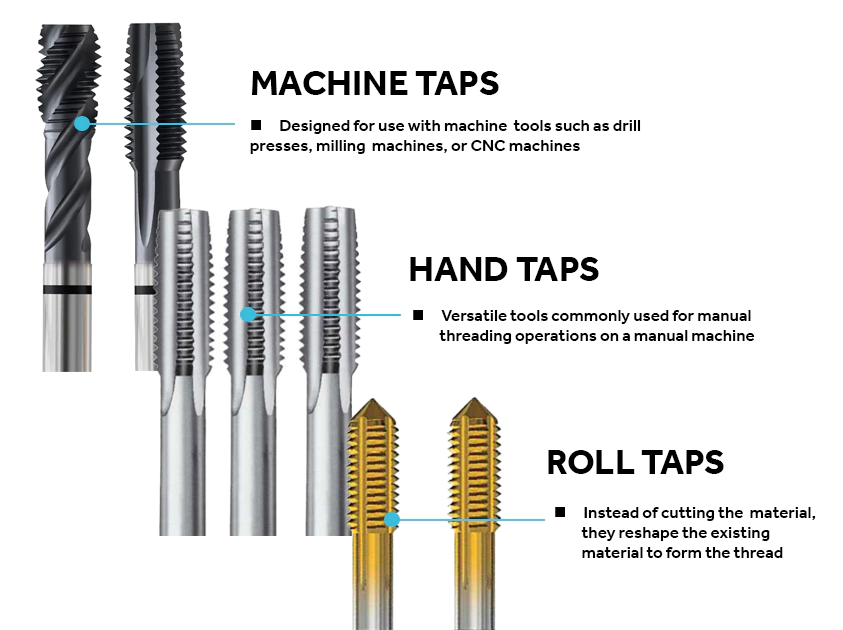
Tap Materials:
Machine taps are typically made from high-speed steel (HSS) or cobalt alloys. HSS taps are suitable for a wide range of materials, including mild steel, stainless steel, aluminum, and brass. Cobalt taps, which contain a higher percentage of cobalt, offer improved hardness and heat resistance, making them suitable for harder materials like alloy steels and stainless steels.
Tap Sizes and Thread Standards:
Machine taps come in a variety of sizes, which are specified by thread diameter, pitch, and thread type. Common thread standards include metric, UNC (Unified National Coarse), UNF (Unified National Fine), and BSP (British Standard Pipe). It’s important to choose a tap that matches the thread specifications of the fastener you intend to use.
Tap Chamfers:
Machine taps have different chamfer styles, which determine the taper at the front end of the tap. The most common chamfer styles are taper (starting thread), plug (intermediate thread), and bottoming (full thread). The choice of chamfer style depends on the depth of the hole being tapped and the desired thread engagement.
Tap Sets:
Machine taps are often sold in sets that include multiple taps of the same size but with different chamfer styles. Tap sets provide flexibility and convenience, allowing you to start with a taper tap, followed by a plug tap, and then finish with a bottoming tap for complete thread formation.
Tapping Methods:
There are different methods for using machine taps:
Hand Tapping:
In hand tapping, the tap is manually turned using a tap handle or tap wrench. This method is suitable for smaller holes or when only a few threads need to be created.
Machine Tapping:
Machine tapping involves using a tapping machine or a drill press with a tapping attachment. The machine provides consistent and controlled rotational speed and feed, making it ideal for larger production runs or when precision is required.
Thread Depth and Hole Preparation:
When tapping, it is important to consider the desired thread depth. The hole should be drilled to the appropriate depth to accommodate the full thread length. It’s also crucial to ensure the hole is properly aligned and perpendicular to the workpiece surface to achieve accurate and straight threads.
Thread Repair:
Machine taps can also be used for thread repair. In cases where threads are damaged or stripped, specialized taps called thread repair taps or thread inserts, such as helicoil inserts, can be used to restore the thread integrity.
Tap Maintenance:
Proper tap maintenance is essential for prolonging the tool’s life and optimizing its performance. This includes regular cleaning, lubrication, and periodic inspection for wear or damage. Dull or damaged taps should be replaced to ensure quality thread production.